(MENAFN – NewsBytes)
In what Ford calls an industry first, the company is using the new technique to mass-produce fuel line clips for its F-250 trucks.
3D printing is an additive manufacturing process that adds material layer by layer to create parts instead of traditional subtractive methods of removing material. This means that less material is naturally wasted.
However, waste still occurs in the form of faulty or defective prints, calibration prints, and spools for filaments.

The company’s 3D printing technologies require material inputs in a variety of physical forms such as powders, liquids, and filaments.
However, pressure drops and the unused raw material cannot be immediately reused for injection molded fuel line clips.
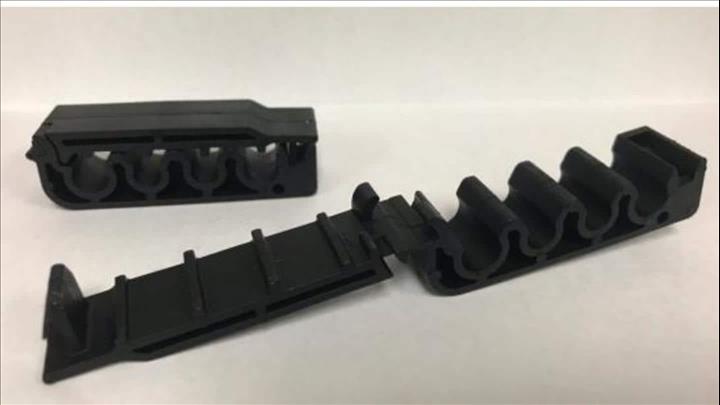
The company converts discarded powder and prints from Ford’s factories into pellets.
These pellets are molded into fuel line clips by Ford supplier ARaymond, which are also used in the design, construction and manufacture of assembly systems.
Ford has also partnered with SmileDirectClub, an oral care and medical technology platform.

However, automakers typically use ABS plastic, nylon, and polycarbonate for prototyping. These materials are denser than injection molded auto parts, which are generally made from PVC, polyurethane, and polypropylene.
So when the denser recycled raw material is injection molded, the resulting parts cannot possibly be lighter.

These used 3D printed parts are also collected and recycled to increase pellet production volume for Ford.
While the new zero-waste approach is a small tweak, given the size of Ford’s operations, it could have a significant impact.
MENAFN27032021000165011035ID1101820354
Disclaimer: MENAFN provides the information “as is” without any guarantee. We assume no responsibility or liability for the accuracy, content, images, videos, licenses, completeness, legality, or reliability of the information contained in this article. If you have any complaints or copyright issues related to this item, please contact the above provider.